In this series, members of the PICK-PLACE consortium are portrayed. After TOFAŞ, ULMA Handling Systems, Mondragon Assembly, IK4-TEKNIKER and CNR-STIIMA, the last partner profile is dedicated to Fraunhofer IFF. Senior research scientist Veit Müller answers the interview.
What is Fraunhofer IFF?
The Fraunhofer Institute for Factory Operation and Automation IFF is an autonomous institute in the nonprofit Fraunhofer-Gesellschaft, the largest applied research organization in Europe. The Fraunhofer IFF specializes in research and development in the fields of robotics, sensor systems, virtual engineering, logistics, and process and plant management. The Fraunhofer IFF’s Robotic System Business Unit is involved in the PICK-PLACE project.
The Fraunhofer IFF’s Robotic Systems Business Unit has extensive experience developing, engineering and integrating robotic technologies and systems used in challenging environments. It works on tactile sensing, safe mobile manipulators, safe workspace monitoring, biomechanical limits for safe human-robot collaboration, and computer-aided safety for better planning industrial applications employing collaborative robots.
The Fraunhofer IFF’s close work with industry puts it in an ideal position to spot current technological needs that can be addressed in the future. The proposed technologies for smart grasping and manipulation of unidentified objects are a prime example with great potential for future commercialization through licensing and knowledge transfer.
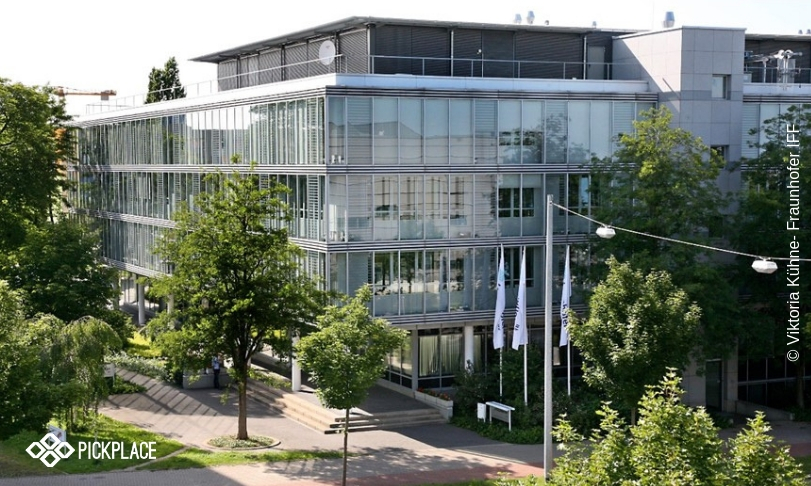
Fraunhofer IFF’s headquarters in Magdeburg, Germany.
How did you learn about PICK-PLACE and why did you decide to join the project?
The Fraunhofer IFF and IK4-TEKNIKER have successfully collaborated in different fields of robotics in the past. That was why TEKNIKER invited us to be part of the PICK-PLACE project. We are mainly contributing our expertise in the field of tactile manipulation.
The first time we picked up the idea of using force feedback information from tactile grippers was in an EU-funded project called pickit. Data on pressure distribution on gripped objects proved useful for online grasp validation, in-hand object pose estimation (when an object is in the gripper) and object shape reconstruction for improved object recognition, for instance, whenever data from a camera is insufficient. Since sensors often have to be designed compactly, especially for adequate hardware integration, we improved on this idea in the ColRobot-project. We designed a compact tactile sensor module with relatively high spatial sensor resolution for sensitive grasping and classification of different types of screws.
The PICK-PLACE project is the logical next step in the technological development while expanding its uses to diverse picking operations in industrial environments.
As one of the technical partners in the project PICK-PLACE, how would you define its main goals and progress beyond the state of the art?
The PICK-PLACE project combines different needs and requirements of flexible and reliable part handling and accurate material placement in unstructured environments such as warehouses. Advanced technologies and innovative system solutions such as adaptive, multifunctional grippers and multimodal sensory systems as well as intuitive human-robot collaboration workspaces are important contributions to that development. Altogether, these solutions can manage the high product variability associated with autonomous pick-and-place applications.
One of the most important technical results expected from the PICK-PLACE project, is the significant development of object recognition with multimodal sensing approaches such as the utilization of vision data and force-feedback data from grasps to expedite the introduction of new and unidentified parts in warehouses.
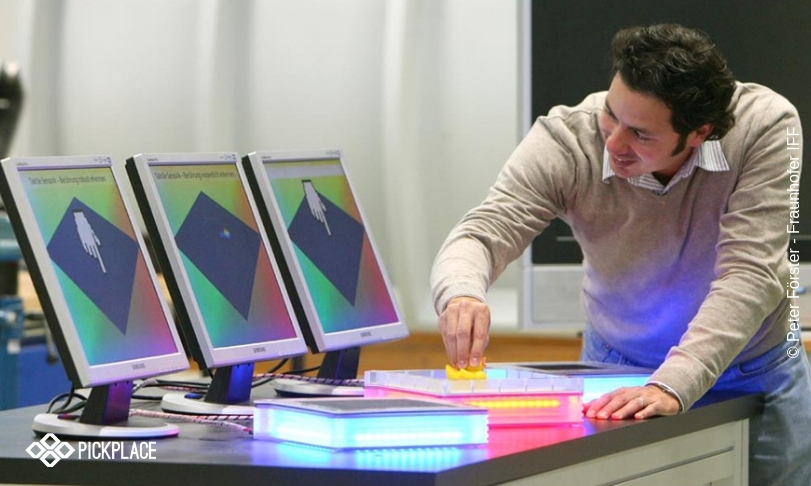
A researcher from Fraunhofer IFF working on object recognition.
In the case of Fraunhofer IFF, what is your main contribution to PICK-PLACE? How do you expect to benefit from it?
I am a senior research scientist in the Fraunhofer IFF’s Robotic Systems Business Unit where I research and develop tactile sensors. Our developments in that field range from different robotic sensing applications such as tactile robot skin, tactile flooring, pressure-sensitive switches and tactile grippers. Our future developments will not only focus on sensor engineering but also incorporate versatile processing of (sparse) tactile sensor data, for instance, from grasps or from pressure profiles on tactile flooring.
In the PICK-PLACE project, I am in charge of coordinating work on the development of flexible grasping tools and sensitive robotic grasping capabilities. This includes developing and implementing tactile sensing in robot grasping, incorporating sensitive manipulation capabilities such as the adoption of gripper motion planning, and improving the picking system’s reliability.
What are your views regarding pick-and-place in your area? Could you mention any other interesting projects in this area?
Flexible feeding operations in general and small-sized companies with high product variability in particular often use robots very little because they are not cost effective. Demand for commercially available, affordable and adaptive robotics solutions is quite high and is addressed by the PICK-PLACE project. Some other interesting projects include:
- SAFELOG: http://safelog-project.eu/
- COVR: http://safearoundrobots.com/
- SUITCEYES: https://suitceyes.eu/
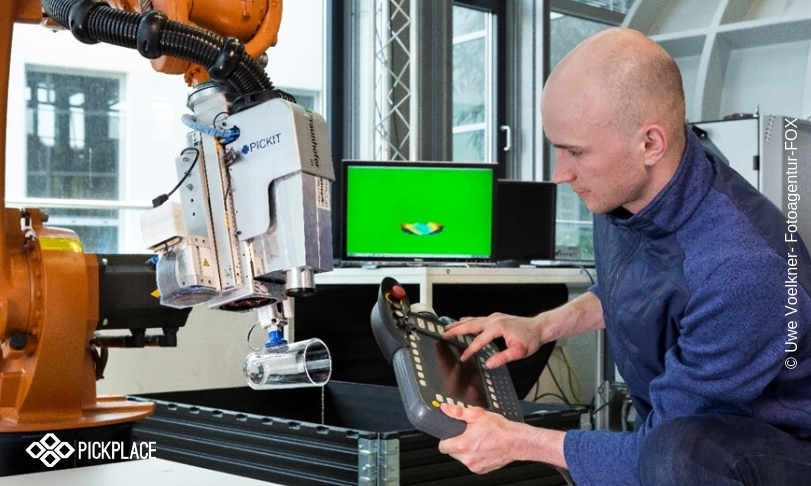